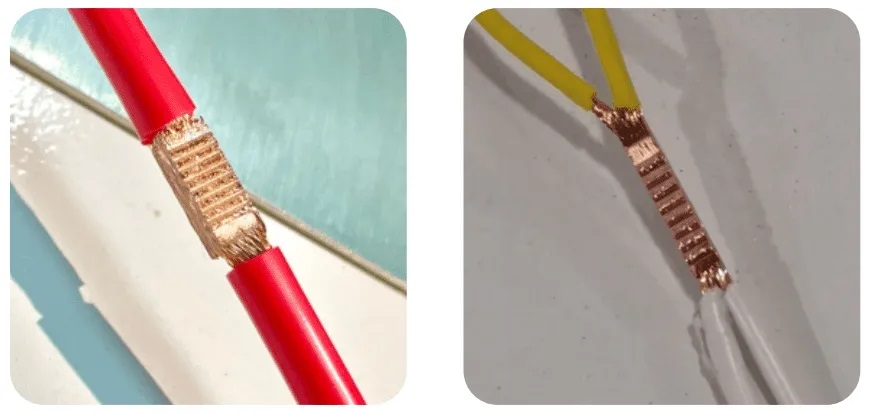
In
the ever-evolving landscape of electronic manufacturing, precision, efficiency,
and reliability are paramount. Among the array of cutting-edge technologies
reshaping this industry, ultrasonic welding stands out as a cornerstone method
that continues to revolutionize production processes. As the demand for
smaller, lighter, and more intricate electronic components grows, the function
and importance of ultrasonic welders become increasingly evident.
What is an Ultrasonic
Welder?
Ultrasonic welding is a bonding technique that
utilizes high-frequency ultrasonic vibrations to create solid-state welds
without the need for additional connective materials such as adhesives or
soldering. This process involves applying high-frequency mechanical vibrations,
typically in the range of 20 to 70 kHz, to the components being joined. These
vibrations generate localized heat and pressure, causing the materials to fuse
together at a molecular level.
The Function of
Ultrasonic Welders in the Electronic Industry:
1. Precision Bonding:
Ultrasonic welders offer unparalleled precision,
enabling manufacturers to create strong and reliable bonds between delicate
electronic components with micron-level accuracy. This precision is crucial in
applications where even the slightest deviation can compromise performance or
functionality.
2. Versatility:
Ultrasonic welding is a versatile process capable
of bonding a wide range of materials commonly used in the electronic industry,
including thermoplastics, metals, and even certain composites. This versatility
allows manufacturers to streamline production processes by eliminating the need
for multiple joining techniques.
3. Rapid Assembly:
With cycle times typically measured in fractions
of a second, ultrasonic welding facilitates rapid assembly of electronic
components, making it ideal for high-volume manufacturing environments. This
speed not only increases productivity but also reduces overall production
costs.
4. Clean and
Efficient:
Unlike traditional bonding methods such as
soldering or adhesive bonding, ultrasonic welding produces clean, precise welds
without the need for additional consumables or post-processing. This results in
a more efficient manufacturing process with minimal waste generation.
The Importance of
Ultrasonic Welders in the Electronic Industry:
1. Miniaturization:
As electronic devices continue to shrink in size,
the demand for precise, reliable bonding techniques becomes increasingly
critical. Ultrasonic welding enables manufacturers to assemble miniature
components with unparalleled accuracy, driving the ongoing trend towards
miniaturization in the electronic industry.
2. Enhanced Product
Performance:
The quality and reliability of electronic devices
heavily depend on the integrity of their internal components. By ensuring
strong, durable bonds, ultrasonic welders play a pivotal role in enhancing
product performance and longevity, ultimately contributing to customer
satisfaction and brand reputation.
3. Cost Efficiency:
In an industry characterized by intense
competition and cost pressures, optimizing manufacturing processes is essential
for maintaining profitability. Ultrasonic welding offers a cost-effective
solution by reducing labor requirements, minimizing material waste, and
streamlining production workflows.
4. Compliance with
Industry Standards:
With stringent regulations governing the safety
and performance of electronic products, manufacturers must adhere to rigorous
quality standards throughout the production process. Ultrasonic welders provide
a reliable method for achieving consistent, high-quality welds that meet or
exceed industry specifications.
Conclusion:
Recent Comments